ALLGAIER
Tumbler Screening Machines TSM / tsi
For intelligent fine particle screening
The highly developed genuine Allgaier tumbler screening machines have set the standard for fine and ultra-fine screening technologies of all types of dry bulk material. Modified and improved design features already successfully applied to the TSM product line are now implemented to the entire tsi product line as well. Featuring 9 different machine sizes ranging in diameters from 600 to 2,900 mm Allgaier currently offers the widest product range of tumbler screening machines available on the market worldwide.
Introducing the world’s largest tumbler screening machine the tsi 290 combined with a number of patented new features such as fully segmented screen inserts Allgaier has extended once again its technological leadership even further.

Industrial Applications
• Chemicals/Pharmaceuticals
• Aggregates and Ores
• Food
• Waste/Recycling
• Plastics
• Metallurgy
• Wood/Biofuels
• Ceramics
• Feed
Technical and process related advantages
• Screening efficiency up to 99% achievable
• No particle destruction of sensitive products due to gentle screening
• Higher specific screening performance in comparison to purely vibrating systems due to higher screening amplitude
• Stable screen motion even at full load
• The steplessly adjustable tumbling motion enables precisely controlled particle retention of the product on the screen enabling screening capacity and efficiency to be balanced to the optimum
• The three dimensional screen motion can easily be recorded enabling reproducible operating conditions to provide a constant high product quality
• Large variety of product specific mesh cleaning systems are available
• Rapid screen replacement systems optionally available
• Modular elements system allow multiple machine concept variety
• ATEX approved machine models available
• Dustproof construction, even gas tight machine models available
• Low noise and low vibrating operation
• Maintenance friendly
Unique tumbling type motion
The adjustment of the machine in response to the product to be screened provides an exactly defined three dimensional eccentric motion pattern with radial and tangential inclination. During operation of the tumbler screening machine the radial inclination causes the product on the screen to move from the centre towards the edge of the screen while the tangential inclination leads to a circular motion of the product on the screen. The combined impact of both of these forces causes the product in a helical motion of upon the surface of the screen and therefor to a relatively long retention time. This provides an optimized result on fraction separation while at the same time minimizing the amount of remaining outsize particles.



ATEX approvals
ATEX approved machine models are available i.e. when operating the machine with explosively hazardous dust products or operating the machine in explosively hazardous areas further in presence of explosively hazardous atmospheric ambient outside or inside of the machine. Following explosion proof design certifications can be issued as per EC-type examination certificate IBExU12ATEX1095X according to RL 94/9/EG:
• For dry screening: II 1 / 2 D c T X
• For dry screening with additional Category 2G related to the equipment outside: II 1D / 2DG c IIB T X
• For dry screening in presence of combustible gases/vapours (hybrid-mixtures): II 1DG c T3 / 2DG c IIB T X
Customer testing centre
Based on more than 20,000 performed test runs Allgaier ensures over decades reliable and efficient screening solutions. By performing deliberated screening procedures in our testing laboratory Allgaier determines the most suitable machine configuration for each individual application.
Options
• Internal screen inserts featuring replaceable slip-over edge sealings
• Machined screen frames equipped with O-Ring gasket i.e. for the pharmaceutical industry
• Fully segmented screen inserts optional with ultrasonic screen cleaning devices
• Mild steel and various stainless steel machine models
• Surface qualities ranging from glass beaded via grinded versions all the way to electrically polished finish
• Food grade elastomer parts (i.e. sealings, covers, etc.)
• Food grade glue for mesh cloth fixation on the screen frames
• Manual or pneumatic deck lifting devices
• Various mesh cleaning systems (ball-, ultrasonic-, air- and brush cleaning devises as well as combined cleaning systems)

Our robust machine
A specially designed, robust “Heavy-Duty” version featuring re-enforced bearings was developed to meet the rugged requirements of the minerals industry.
Our machine for demanding applications
The VA tumbler machine available in several stainless steel models meets highest demands within the chemical, pharmaceutical and food industries regarding corrosion protection.

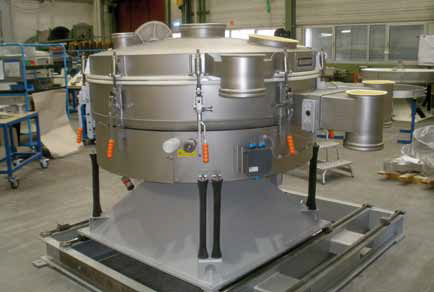
Types | TSM 600 | TSM 950 | TSM 1200 | TSM 1600 | |
Diameter | mm | 650 | 1,050 | 1,250 | 1,580 |
Screen area per deck | m² | 0.28 | 0.72 | 1.10 | 1.80 |
Net space requirement | m² | 0.36 | 1.20 | 1.57 | 2.50 |
Rated electr, power | kW | 0.25 | 1.50 | 1.50 | 4.00 |
Mesh cleaning systems | |||||
Bouncing ball cleaning | • | • | • | • | |
Ultrasonic cleaning | • | • | • | • | |
Combined ultrasonic and balls | • | • | • | • | |
Air cleaning | • | • | • | • | |
Combined ultrasonic and air | • | • | • | • | |
Brush cleaning | • | • | • | • | |
Combined air and brushes | • | • | • | • | |
Passing unit | • | • | • | • | |
Dimensions | mm/kg | Height/Weight | Height/Weight | Height/Weight | Height/Weight |
1-Deck | 836/145 | 1,044/350 | 1,128/420 | 1,409/820 | |
2-Decks | 943/155 | 1,171/400 | 1,360/480 | 1,574/890 | |
3-Decks | 1,049/165 | 1,290/450 | 1,535/520 | 1,746/960 | |
4-Decks | 1,156/175 | 1,425/510 | 1,714/590 | 1,918/1,040 | |
5-Decks | 1,262/185 | 1,552/580 | 1,890/660 | 2,090/1,120 |
Our largest machine
The tsi 290 is our largest tumbler screening machine. Providing a screen diameter of almost 3 metres the tsi 290 offers an extra screening area
of 20% in comparison to the TSM 2600 model. In addition the low overall height makes the tsi 290 the most economical solution in many applications
when expanding plants where the previously available screening capacity is no longer sufficient.
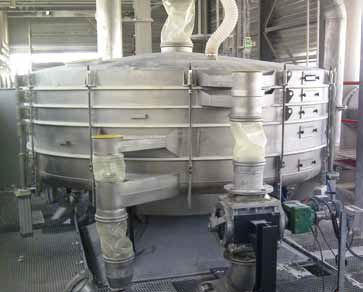
Continuous mesh cleaning guarantees highest screening quality
Due to its round body and its unique drive system the tumbler screening machines are particularly suitable for operating with various types of mechanically driven rotating mesh cleaning
devices.
The screen is continuously cleaned during the screening process ensuring high screening quality and a constantly high product flow.
Bouncing balls
The bouncing ball mesh cleaning device available in several variations is the universal cleaning system for numerous granular products.
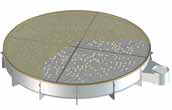
Ultrasonic
Ultrasonic screen cleaning is particularly suitable for applications with fine mesh apertures ranging from 20 to 1,000 μm.

Combined ultrasonic and balls
For a maximum of product throughput trough the screen and permanent mesh cleaning.
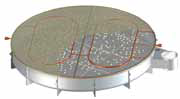
Air Flow
The impact of high speed air flow provided by rotating arms placed directly under the screen is blowing out particles caught in the mesh which is an ideal solution i.e. for sticky products.

Combined ultrasonic and air
Applicable when processing products extremely critical to screen such as fine plastic powders etc.
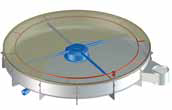
Conical rolling brushes
Rotating conical brushes placed right under the screen clean gentle and with low-wear. Typically used for spherical products blinding the mesh.

Combined air and brushes
This is an effective cleaning system i.e. for greasy or electrostatically charged products.
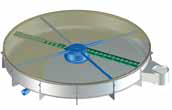
Passing/straining unit
Allow gentle straining i.e. disagglomeration
of products like instant coffee by using steel or
plastic spatulas, rotating on top of the screen.
